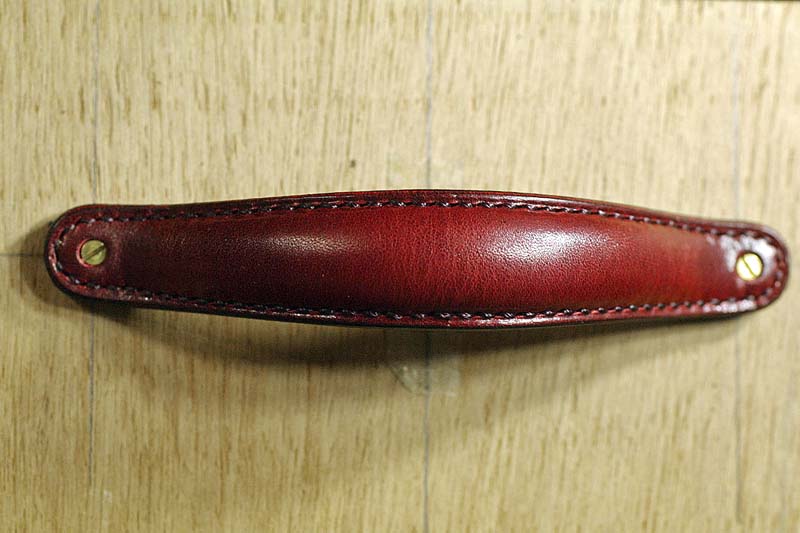
外注
今回は家具屋さんからの革の取っ手の受注案件になります。この場合、当店は家具店に革の取っ手を収める外注という立場になります。外注案件の場合は基本的に受注品の掲載は許可されないのですが、今回はお許しを頂いております。
ただこの記事を掲載し、「これと全く同じものを」という依頼は受けないでくださいと言われているので、ご希望の場合はデザイン変更が必要にはなります。
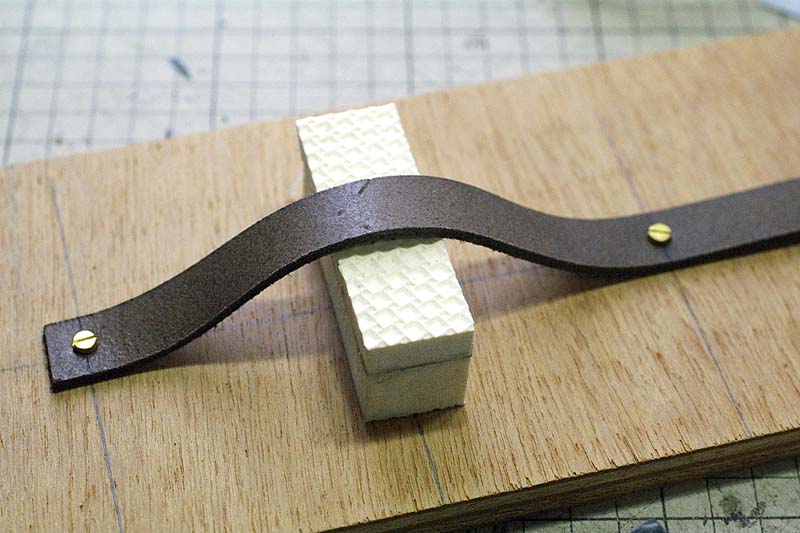
今回のご依頼は家具のオーダーの際に取り付けられる革の取っ手の依頼です。家具をオーダーされたお客様が革の取っ手の色もカスタムできるという展開をされたいということで、革はイタリアのオイルレザーを使うことになり、10色から選択できる展開となりました。縫製に使用する糸の色も好きな色から選択できるようになっています。
図面を頂いてそれに従って製作するのですが、図面には浮かせた状態での横幅の寸法の記載があるだけなので、取り付ける前の伸ばした状態の全長が分からないので、とりあえず浮かせるとどのくらいプラスアルファの長さが必要になるのか平らな革で確認してみます。
試作
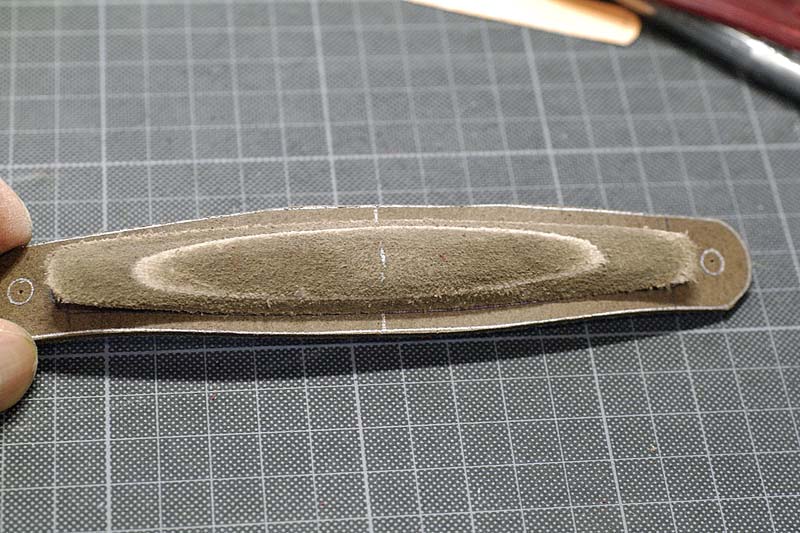
取っ手には厚みと硬さが必要なので芯材にはヌメ革を積み重ね、裏表面をオイルレザーで覆います。芯材にするヌメ革を削り出し、どのくらいの膨らみだと最終的に革をかぶせた時にどのような表情になるのかを試作で確認していきます。
手元にまだ本番の色の革がなかったので同じ厚みで表情と硬さの似たオイルレザーでとりあえず試作をしてみます。糸の太さと縫い目のピッチで見え方が変わってくるので、縫い目サンプルも作りピッチと糸の太さも決めていただきました(縫い目のピッチと糸の太さは固定仕様)
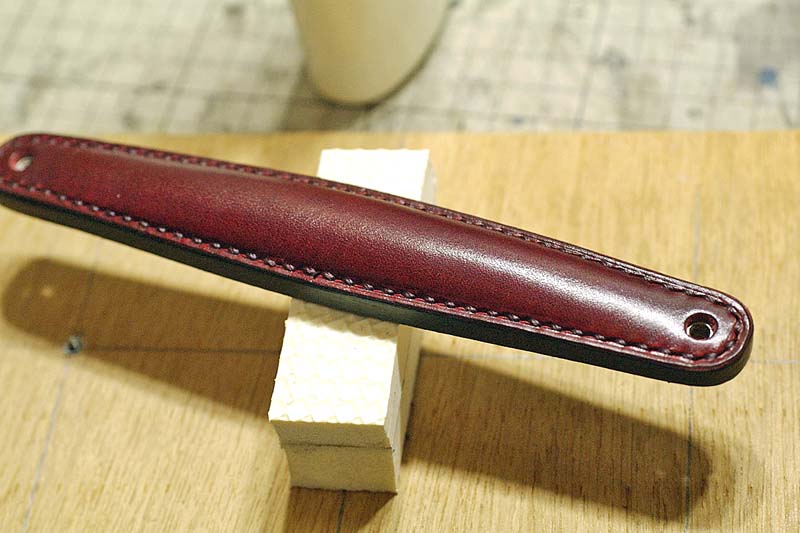
湾曲を手で癖付けしてしまうとそれぞれで膨らみが違ってしまいそうなので、指定された隙間の高さ25mmで台を作り、それを軸に反らせて両側をビスで固定すれば毎回同じ湾曲にすることができます。

よいっしょっと、と四股を踏んでるみたいですが・・・。
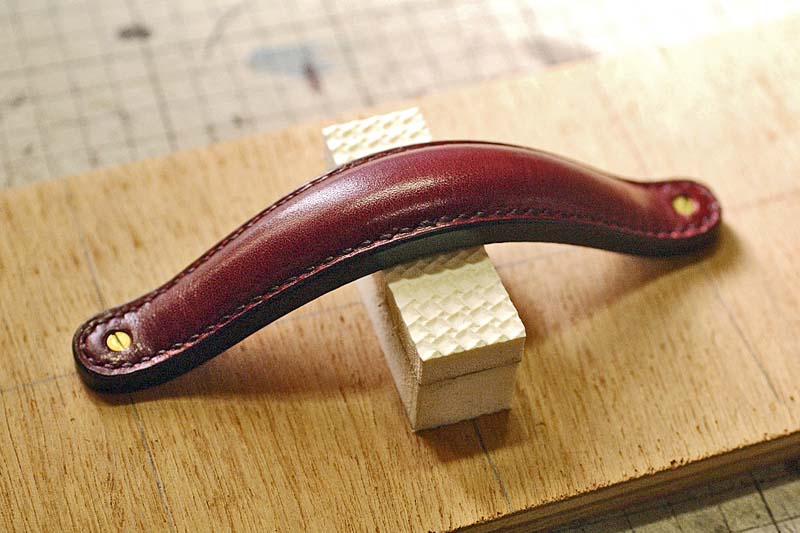
25mmを狙ったのですが26mmの浮きになっています。プラス1.0mmなので革に開けたビスの穴の距離間を1.0mmマイナスにすれば25mmに近ずくと思います。
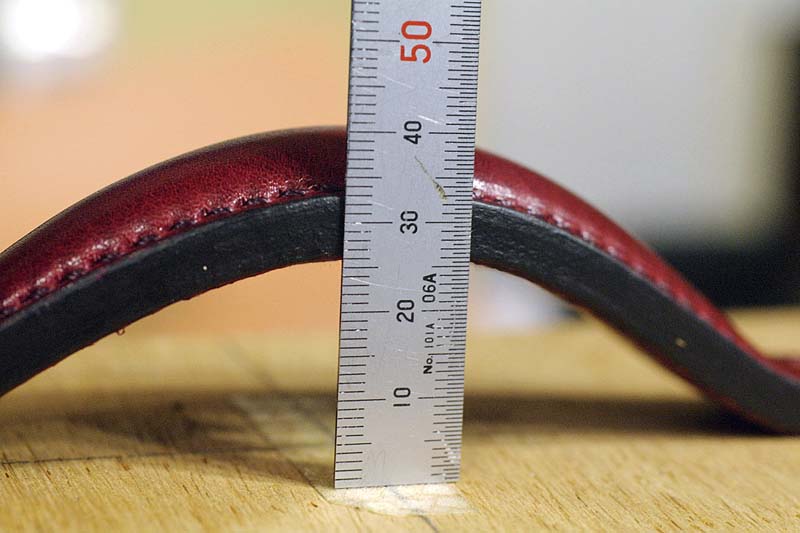
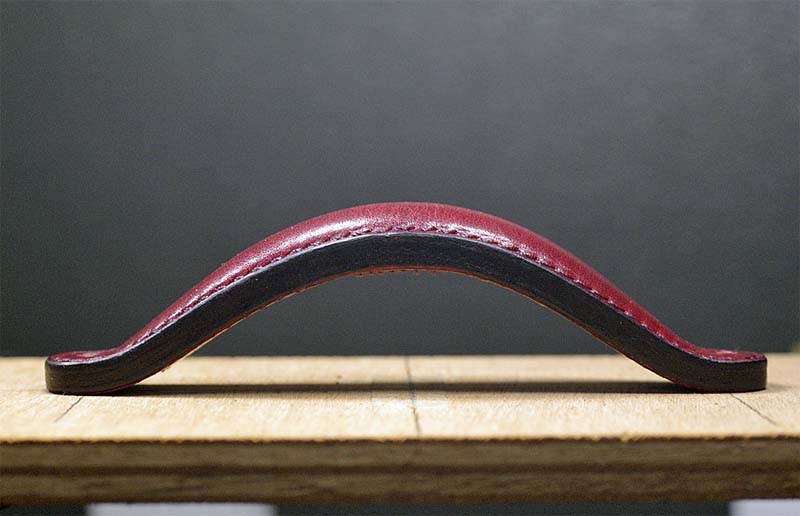
ただ革製品なのでこれぐらいは許容範囲としてみて頂かないと製作は厳しいです。一点ものであればまだ近似値に近づけられますが、毎回複数個の製作となると革の硬さであったり厚みの誤差であったりは天然素材ゆえに必ず違いが生じます。その個体差により、しなりや伸びが違ってくるのである程度の誤差はご容赦頂かないとです。
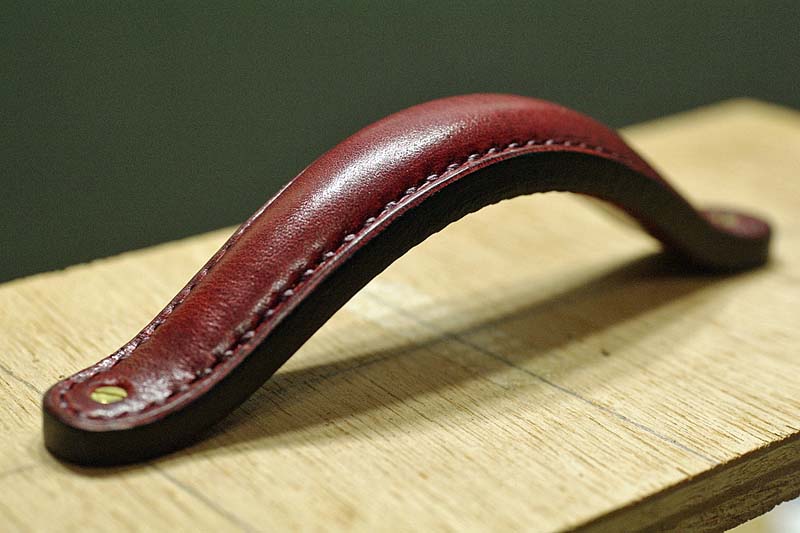
試作により数値データが取れたので、その後に届いた本番の革で2度目の試作を作りご依頼主に送付。確認して頂くと、膨らみ方に修正が入ったので芯材の形状を修正し再び試作して最終確認。そしてようやく本番へ。
組み立て
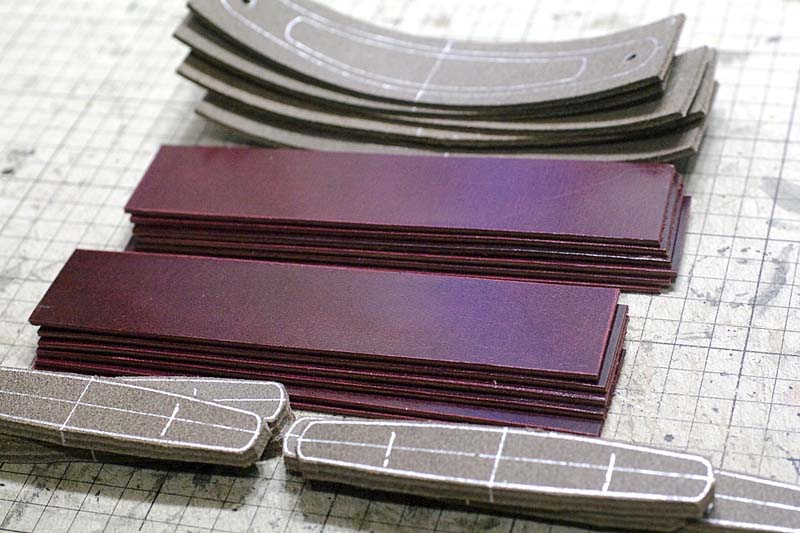
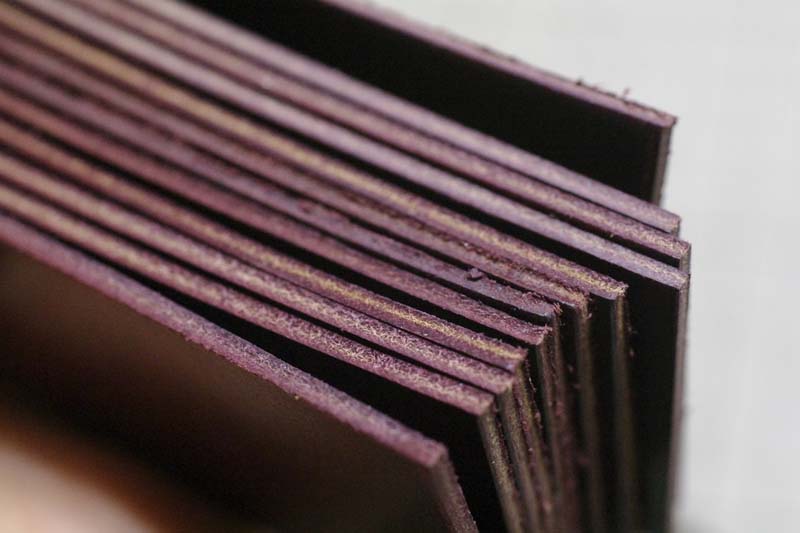
この取っ手で一番大変なのが芯材の削り出し。三次曲面を寸法通りに削り出していくので削ってはノギスで計測し、削ってはノギスで計測し・・・。
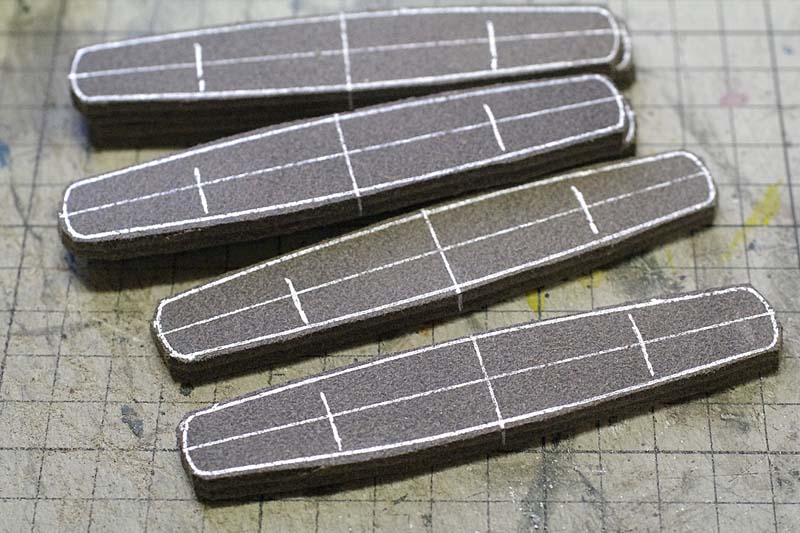
一個削り出すのにどのぐらい時間がかかっているのかを計測してみると・・まずいですね、時間が掛かりすぎています。木材を削るのであればまだ楽なのですが、革って硬いようでいて柔らかいので削っている時も形状が動くので削りにくいです。ノギスで測る時も抑える圧力だったり角度でコンマいくつは変わってしまうので数値に惑わされ気味です。
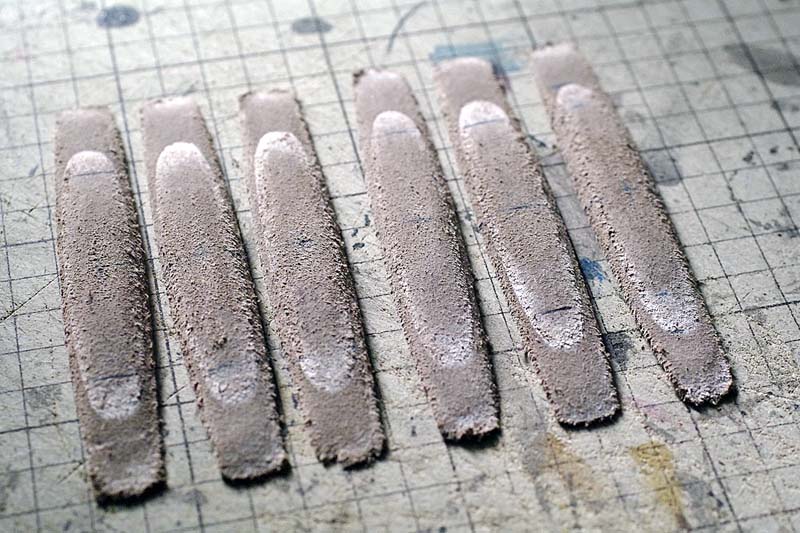
ビスの頭が革に食い込んで抜けてしまわないように積層の間には真鍮のワッシャーを挟み込んでいます。

削り出し
今回使用するイタリアのタンニン鞣しのオイルレザーは、かなりオイルを含有しているので色が凸部分でプルアップします。プルアップとは革が曲げられたり押し出された際に、革に含まれたオイルが繊維の中で動いて色が変化する状態です。
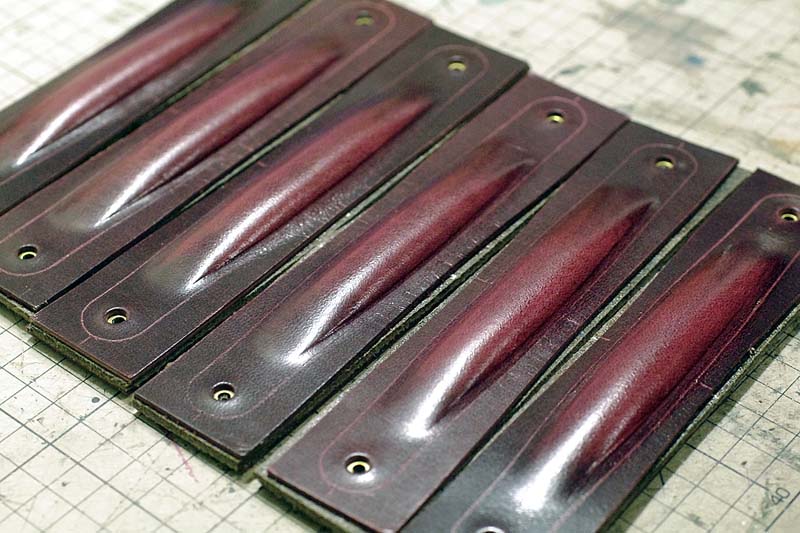
今回の取っ手のデザインを見て、このプルアップレザーを使うとより立体感が出て適しているのではないかということでご依頼主にオススメした次第であります。
オイルを多量に含ませた革だとホーウィン社のクロムエクセルレザーのように表面がしっとりしていて、「オイル含んでいるな」という革もありますが、この革は表面がとてもツルツルすべすべしていて触った感じはオイルコードバンのような質感があります。
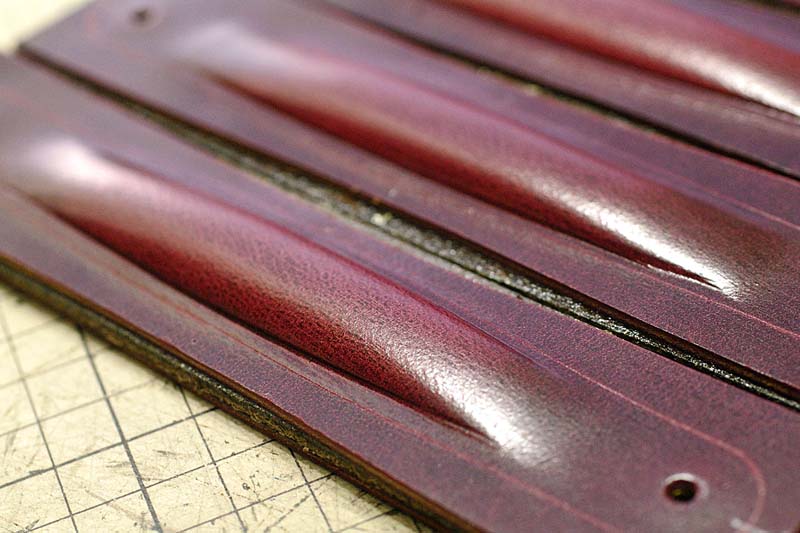
周囲の余分なところを革包丁で荒立ちし、その後は狙った数値めがけてひたすら削り出していきます。
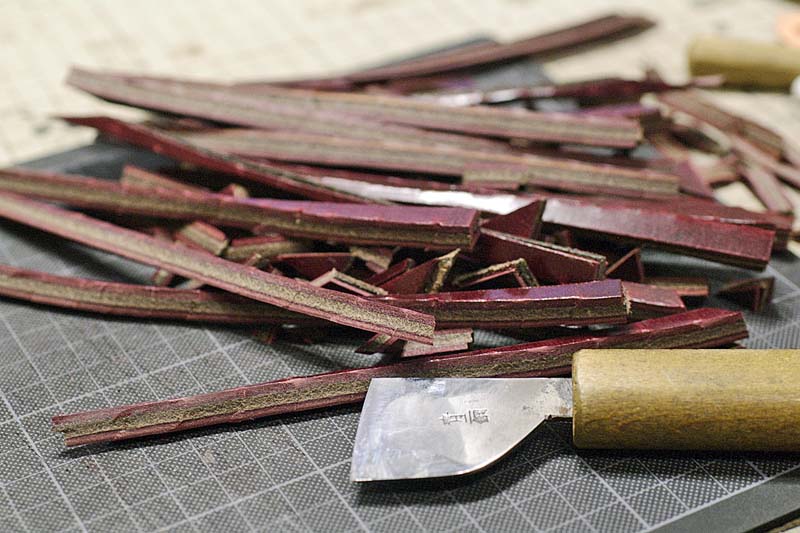
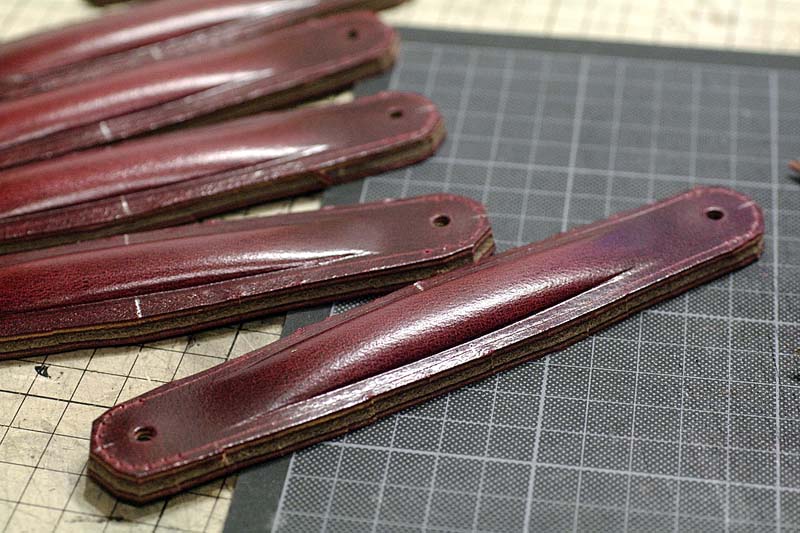
削ってはノギス、削ってはノギスで計測・・・。芯材の削り出しもそうですがこの形状の削り出しもかなり時間が掛かります。なのでもう少し効率化できないかと毎回製作する度に作業工程を見直してはいるのですが・・。
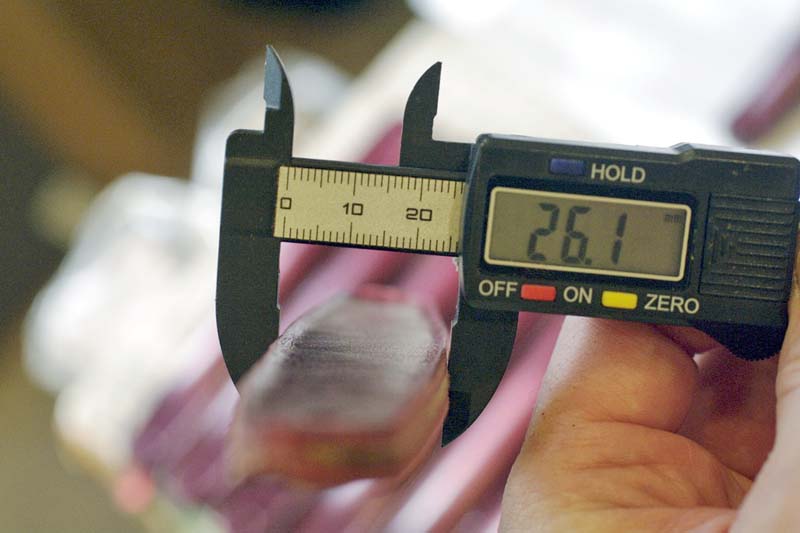
例えば抜き型を作ってしまい、一つ一つ削り出す作業を省略できないだろうか?と。
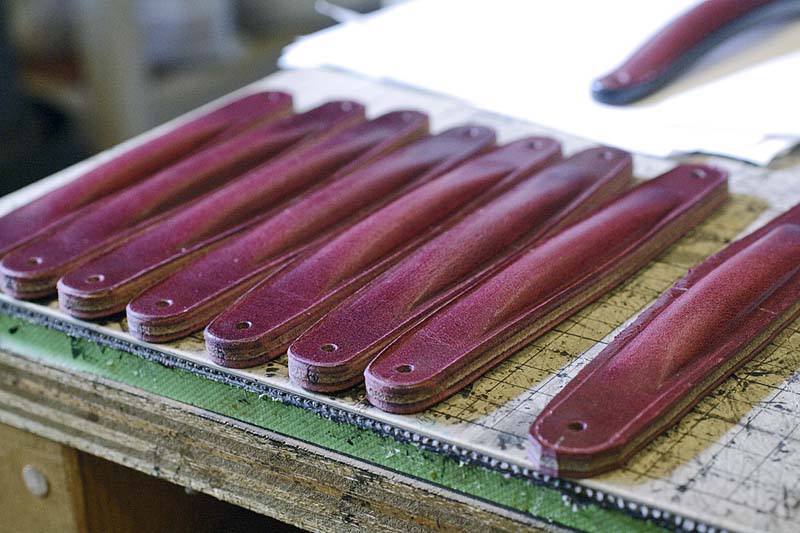
盛り上がった芯材を革で覆うと、その覆い被せ具合でどうしても歪みが生じます。抜き型を使用するにもその歪みを考慮すると仕上がり寸法よりだいぶ大きめな型にするしかありません。歪み方によっては抜ける個体と抜けない個体も出てきてしまいそうなので結局はあまり効率化できないなと。
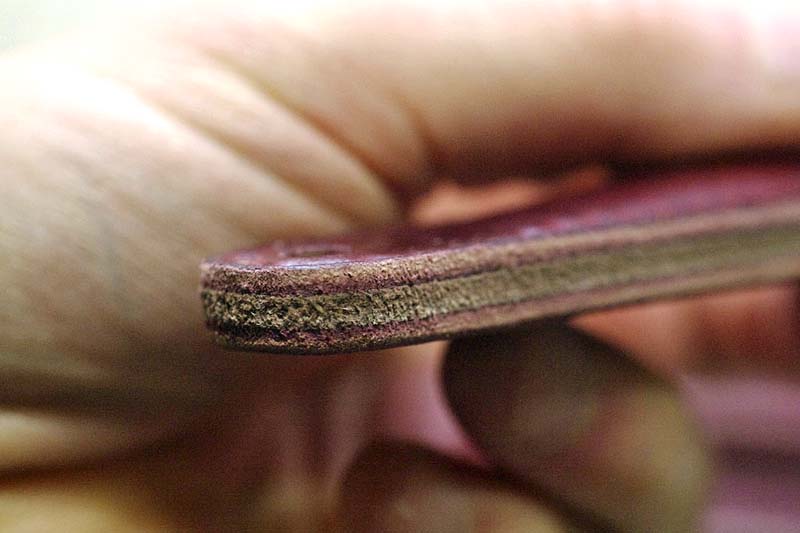
先ほども言いましたが木材であれば削りやすいのですが、革なので固そうでいて柔らかいというのが削るには厄介です。そしてヌメ革の芯材と柔軟なオイルレザーを積層しているので層により革の硬さが違います。硬さが違うものを一緒に削ると硬い素材が凹んだように削れてしまいがちになるので、真ん中あたりを膨らませるようなイメージでちまちま削っていきます。
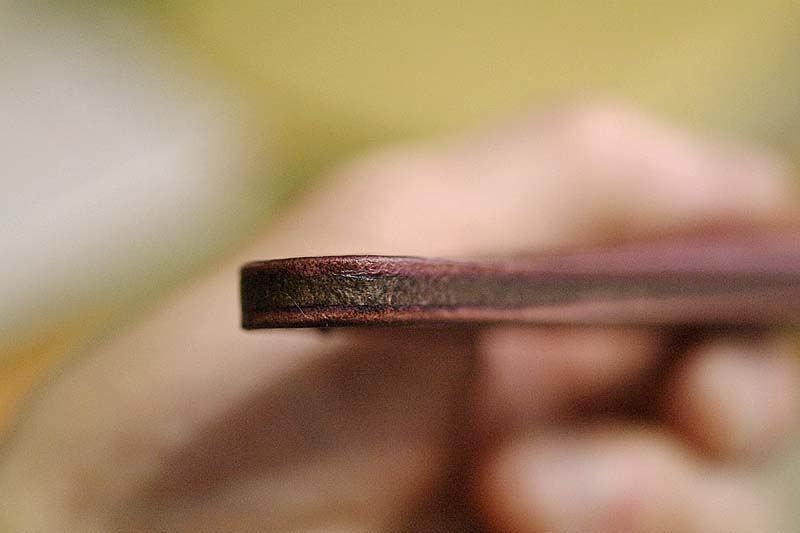
そんなこんなで削り難いなぁと愚痴りながら削りが終了。次にボサついたコバを締めます。この締める作業でも寸法が変わってくるので、この数値の変化も削る工程で計算には入れますが革の個体差があるので誤差は生じてしまいます。
縫製
菱目打ちで縫い目のピッチを印つけていきます。厚みがあるので菱目打ちで貫通させようとすると、おもて面の穴が広がり過ぎてしまいます。なので菱目打ちでピッチを決めて菱錐でひと穴ずつ貫通させていきます。
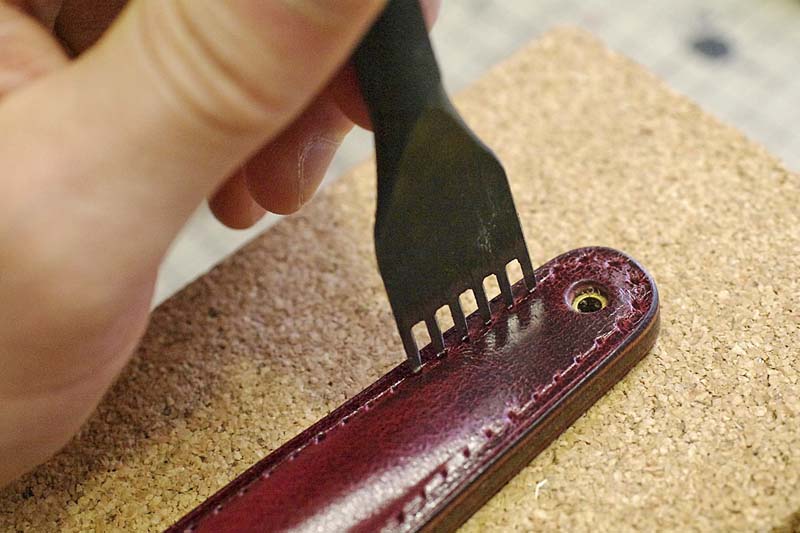
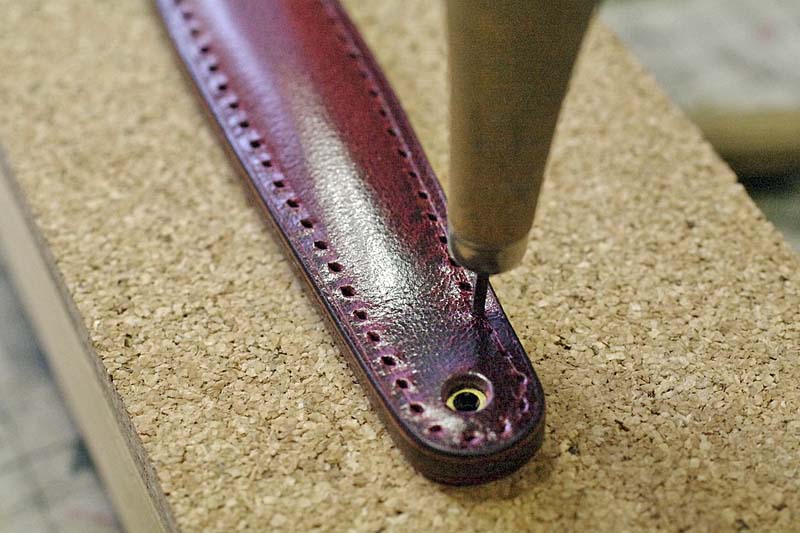
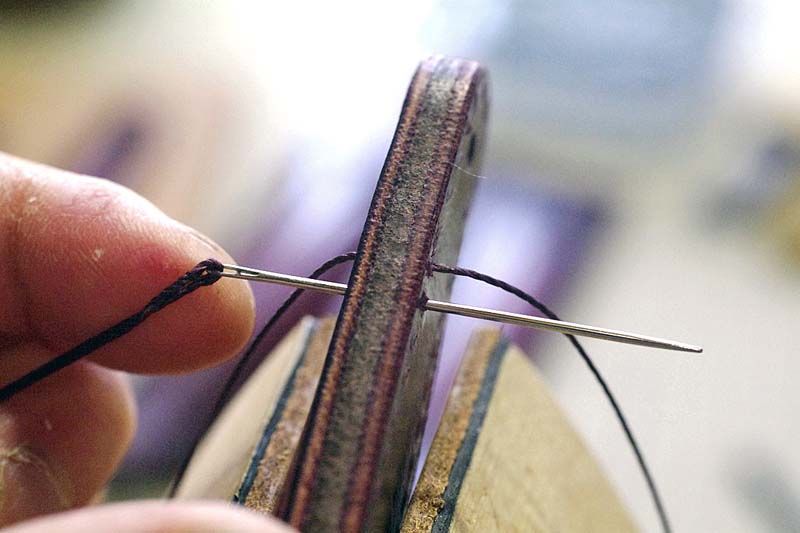
手縫いの場合は一本の糸の両端に針をつけ両面から針を通して縫製していきます。いわゆるサドルステッチといわれているやつです。
馬具の鞍(サドル)を縫製するのに使われている方法という事で、馬を走らせている時に鞍の縫製がほつれて落馬してしまうと大変危険なので、仮に一箇所縫い目が切れても周辺の縫い目が連鎖的に切れ難いという事で、昔からサドルステッチは馬具の縫製に用いられているようです。
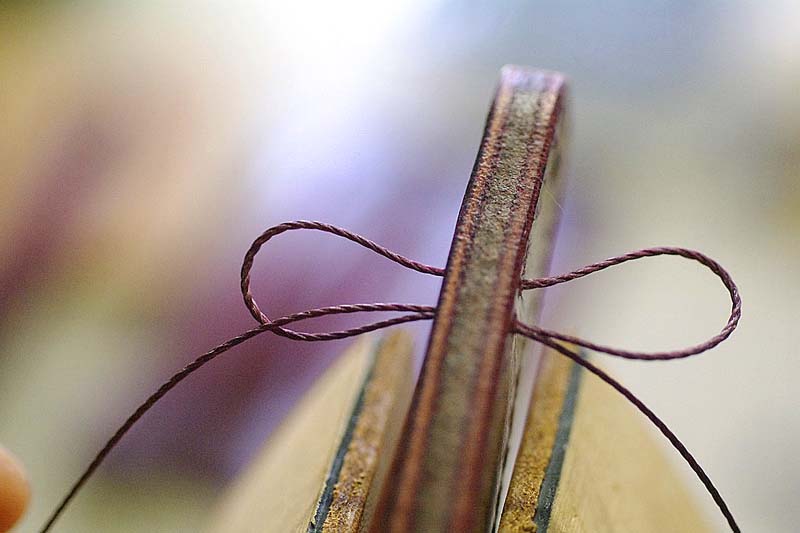
サドルステッチ
拙いですが縫い目の断面図になります。サドルステッチは一本の糸で縫いますが分かりやすくする為に色を分けています。ミシンは上糸が赤糸で下糸が青糸です。
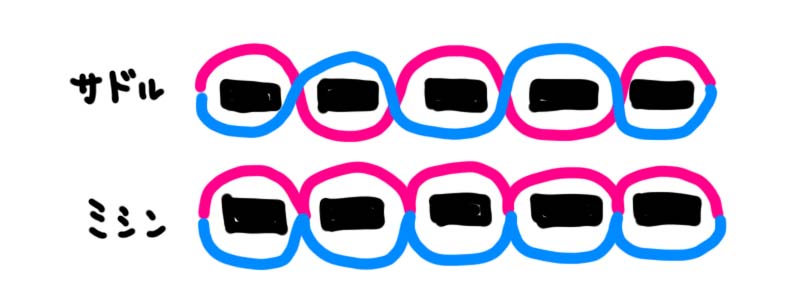
サドルステッチは赤糸がどこか一箇所切れても、反対側から通っている青糸がとりあえず連続して繋がっているので簡単には剥がれないとされています。ミシンの場合は青糸が一箇所切れた場合は、赤糸と穴の中で引っかかっているだけなので切れたところからスルスルと青糸が抜け、青糸が抜けると引っかかっていた赤糸も簡単に抜けてしまいます。
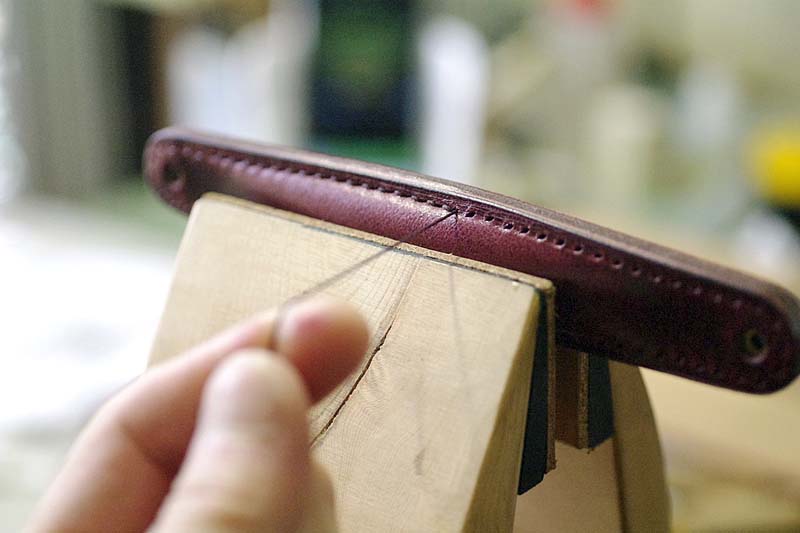
手縫いはミシンに比べると穴を開けてひと穴ひと穴に糸を交差させて縫っていくので大変手間ではありますが、縫い始めるとゾーンというか無心になれるので嫌いな作業ではありません。
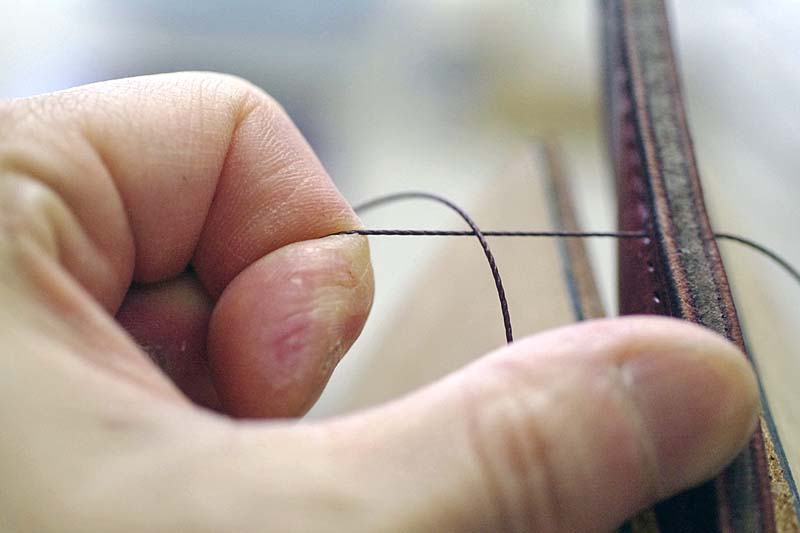
糸を引く時は縫い目が革に食い込み、ぎゅっと沈んでいく感触を指先に感じならが一目、一目と縫っていきます。この小さな個体の中でも革の繊維の詰まり方で硬い部分や柔らかい部分が所々にあります。
革小物であれば大して力を入れて糸を引きませんが、靴底を縫うときにはかなりの力で糸を引くので素手で縫っていると皮膚が裂けるので革の指サックを装着しないとです。
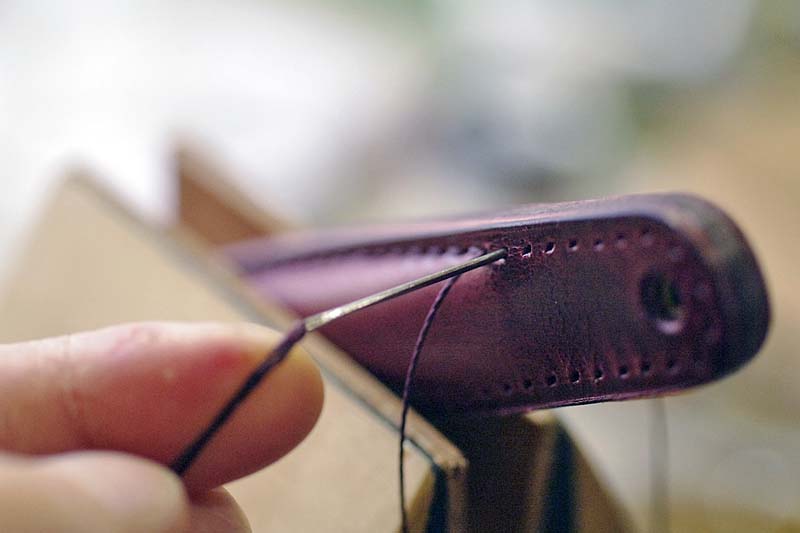
縫い終わったらまた周囲を削ります。縫製することで重なった革が寄せられて層になった断面が僅かにずれるのでそれを整えます。
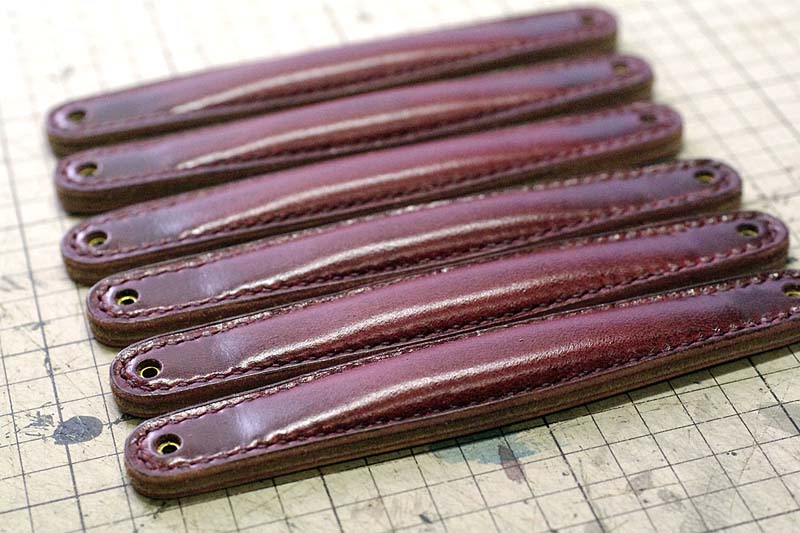
仕上げ
ずれを削って整えたらまたコバがぼさつくので表面を締めます。工程を行ったり来たりしますが革の仕上げっていつもこんな感じです。コバを整えたら次に黒く染めていきます。
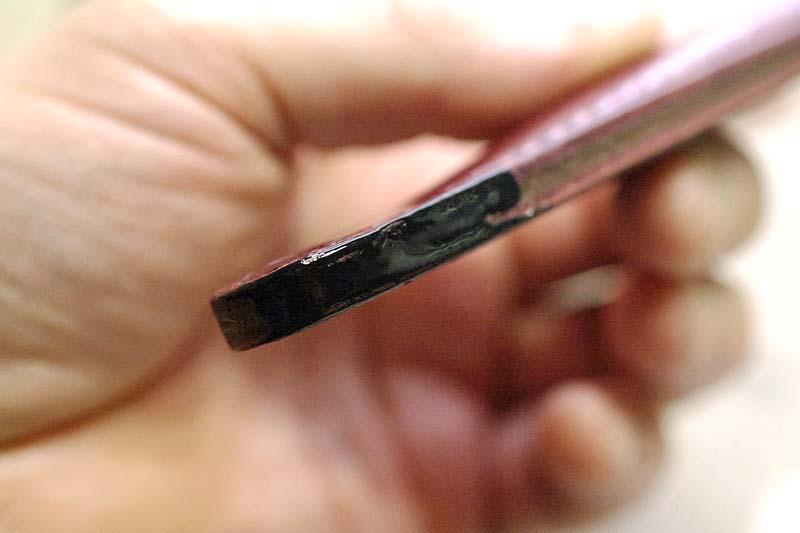
映えさせるために芝の上に置いている訳ではなく、コバに塗料を載せているので机に置いてしまうと塗料が机に付いてしまい、そのまま乾燥させると机に固着されてしまいます。なので固着しないように点で支えるような台が必要になりますが100均で見つけたこの芝生がいい感じです。
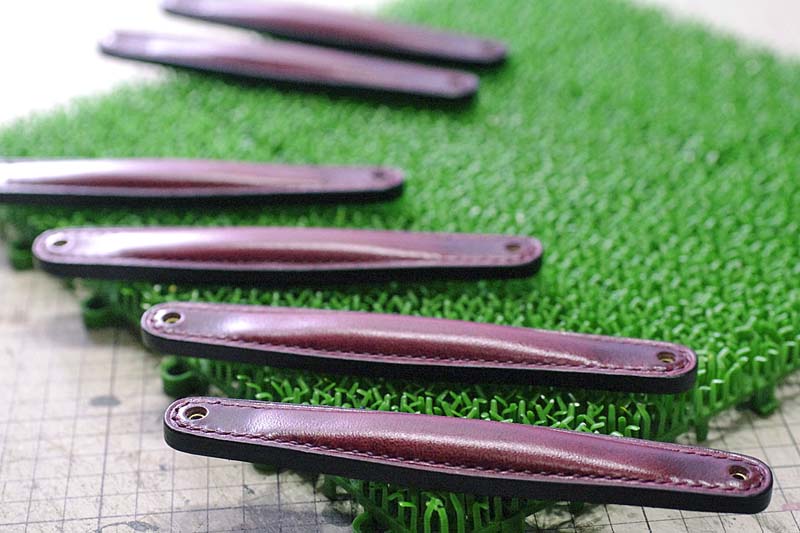
塗料が乾いたら番手の細かい紙やすりでコバを整え、再び塗料を載せまた整えます。最後に色落ち予防と防水効果を兼ねてコバに蝋を溶かし込み磨きあげ、フチに玉捻を入れてキワを引き締めます。
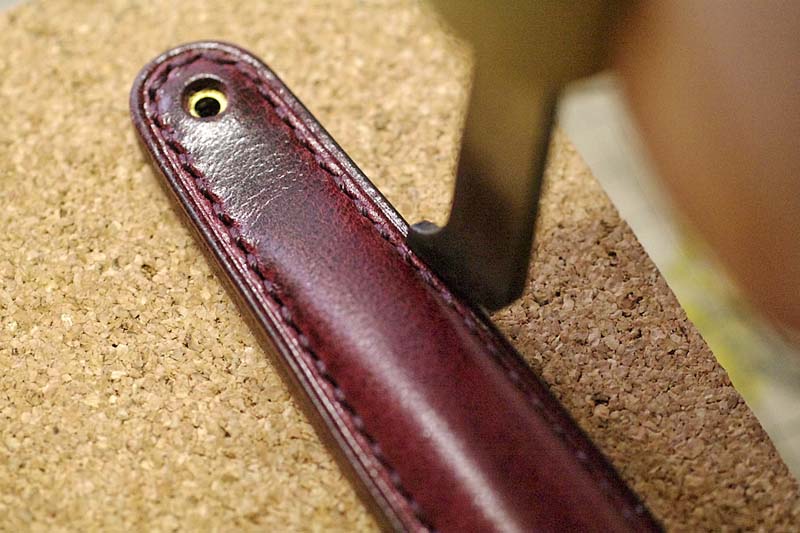
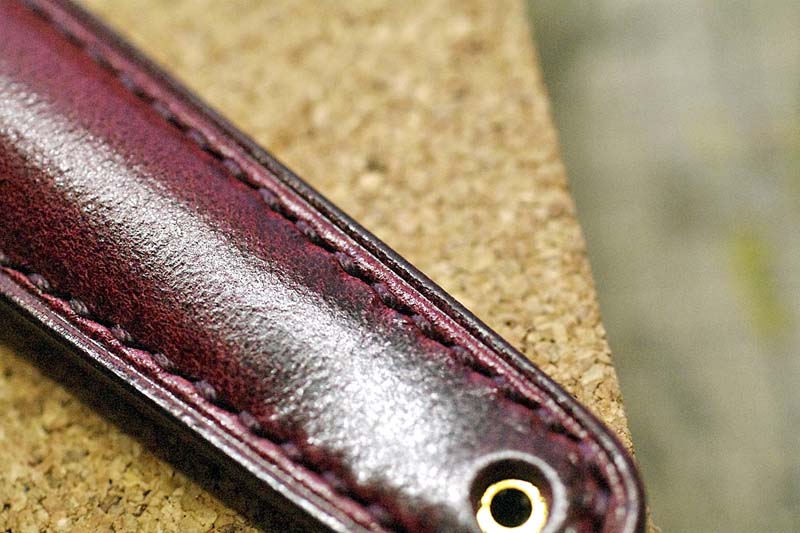
革の取っ手完成
試作を送った後に膨らみの修正が入ったと冒頭で書きましたが、はじめの試作品とこの本番のどこが違うのか?それは初回のサンプルは芯材の膨らみが付け根のネジ穴周辺まで隆起してさせていましたが、その膨らみは中央でピークになりネジ穴周辺ではフラットにする、という修正が入っています。
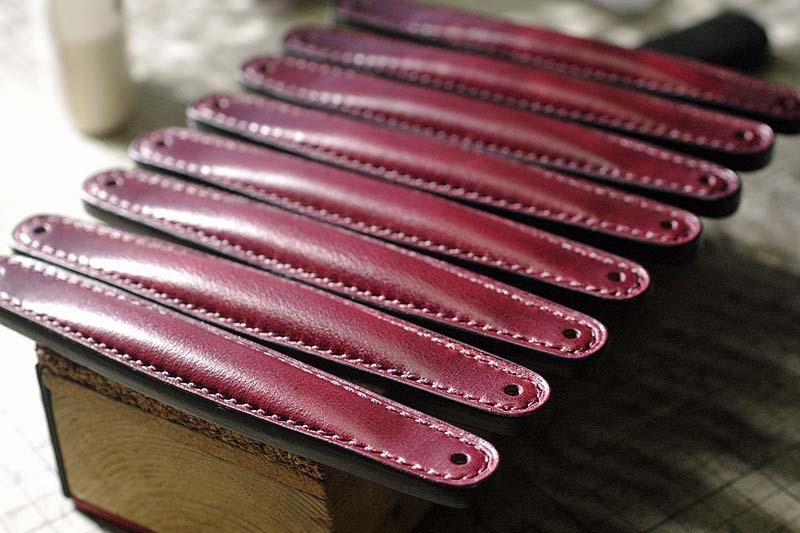
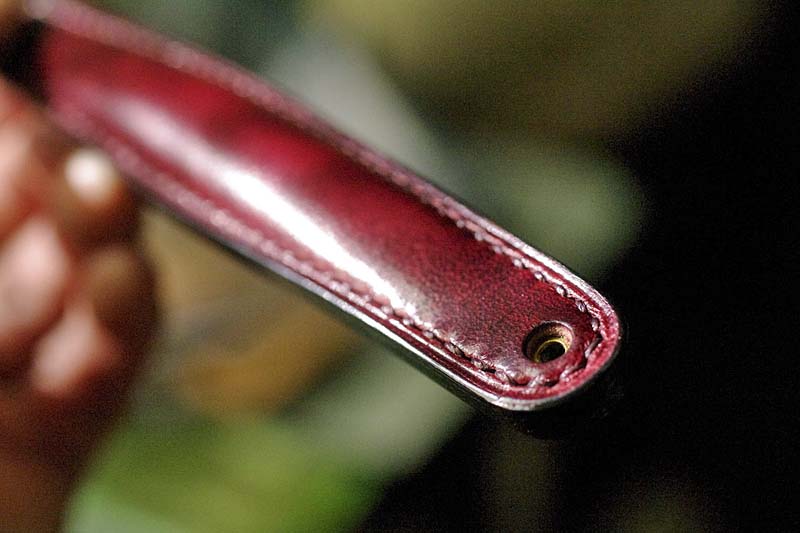
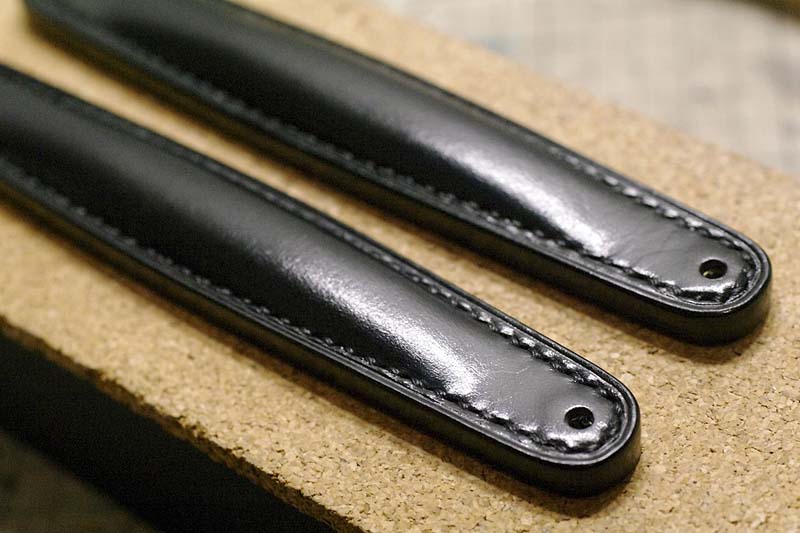
現代の家具の取っ手だと綺麗にメッキされていてエイジングというよりは変化=劣化のように見えてしまいがちですが、革の取っ手であれば日々手に触れることで革が育ち、その変化にも愛着が湧いてくるのではないかと思います。
付属の革のパーツであったりショップの内装であったり小道具であったりと、靴と鞄以外でも色々と製作を承っていますのでお気軽にお問い合わせいただければと思います。